Separation Processes🧪
- Taliya Mammadhasanzada
- Sep 2, 2020
- 9 min read
Warm greetings to all 🤩in the 29th post on #Day29 ! Today, we will continue learning about Separations. Here we go,
Choice of Separator for Homogeneous Fluid Mixtures I – Distillation
SINGLE-STAGE SEPARATION📌
As pointed out in the previous post, the separation of a homogeneous fluid mixture requires the creation of another phase or the addition of a mass separation agent. Consider a homogeneous liquid mixture. If this liquid mixture is partially vaporized, then another phase is created, and the vapor becomes richer in the more volatile components (i.e. those with the lower boiling points) than the liquid phase. The liquid becomes richer in the less volatile components (i.e. those with the higher boiling points). If the system is allowed to come to equilibrium conditions, then the distribution of the components between the vapor and liquid phases is dictated by vapor–liquid equilibrium considerations. All components can appear in both phases. On the other hand, rather than partially vaporize a liquid, the starting point could have been a homogeneous mixture of components in the vapor phase and the vapor partially condensed. There would still have been a separation, as the liquid that was formed would be richer in the less-volatile components, while the vapor would have become depleted in the less-volatile components. Again, the distribution of components between the vapor and liquid is dictated by vapor–liquid equilibrium considerations if the system is allowed to come to equilibrium. When a mixture contains components with large relative volatilities, either a partial condensation from the vapor phase or a partial vaporization from the liquid phase followed by a simple phase split can often produce an effective separation.
DISTILLATION📌
A single equilibrium stage can only achieve a limited amount of separation. However, the process can be repeated by taking the vapor from the single-stage separation to another separation stage and partially condensing it and taking the liquid to another separation stage and partially vaporizing it, and so on. With each repeated condensation and vaporization, a greater degree of separation will be achieved. In practice, the separation to multiple stages is extended by creating a cascade of stages as shown in Figure 9.1. It is assumed in the cascade that liquid and vapor streams leaving each stage are in equilibrium.
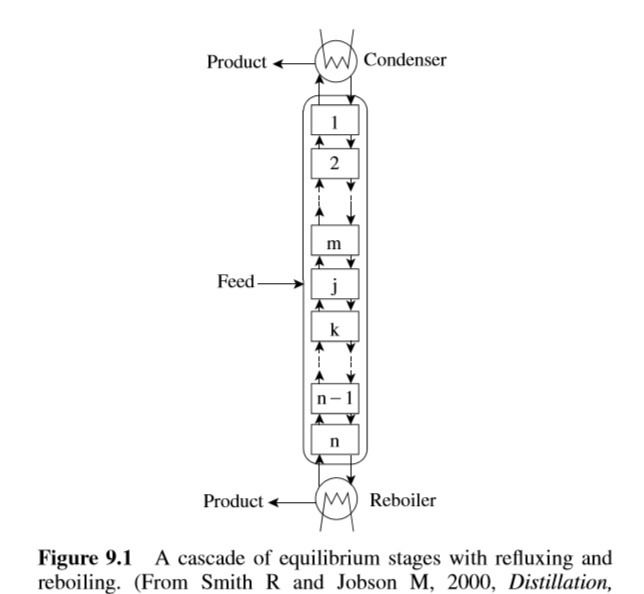
Using a cascade of stages in this way allows the more volatile components to be transferred to the vapor phase and the less-volatile components to be transferred to the liquid phase. In principle, by creating a large enough cascade, an almost complete separation can be carried out. At the top of the cascade in Figure 9.1, liquid is needed to feed the cascade. This is produced by condensing vapor that leaves the top stage and returning this liquid to the first stage of the cascade as reflux. All of the vapor leaving the top stage can be condensed in a total condenser to produce a liquid top product. Alternatively, only enough of the vapor to provide the reflux can be condensed in a partial condenser to produce a vapor top product if a liquid top product is not desired. Vapor is also needed to feed the cascade at the bottom of the column. This is produced by vaporizing some of the liquid leaving the bottom stage and returning the vapor to the bottom stage of the cascade in a reboiler. The feed to the process is introduced at an intermediate stage, and products are removed from the condenser and the reboiler.
Methods📌
The methods by which the vapor and liquid are contacted in each stage of the cascade in distillation fall into two broad categories. Figure 9.2a shows a plate, or tray, column. Liquid enters the first plate at the top of the column and flows across what is shown in Figure 9.2a as a perforated plate. Liquid is prevented from weeping through the holes in the plate by the up-flowing vapor. In this way, the vapor and liquid are contacted. The liquid from each plate flows over a weir and down a downcomer to the next plate, and so on. The design of plate used in Figure 9.2a
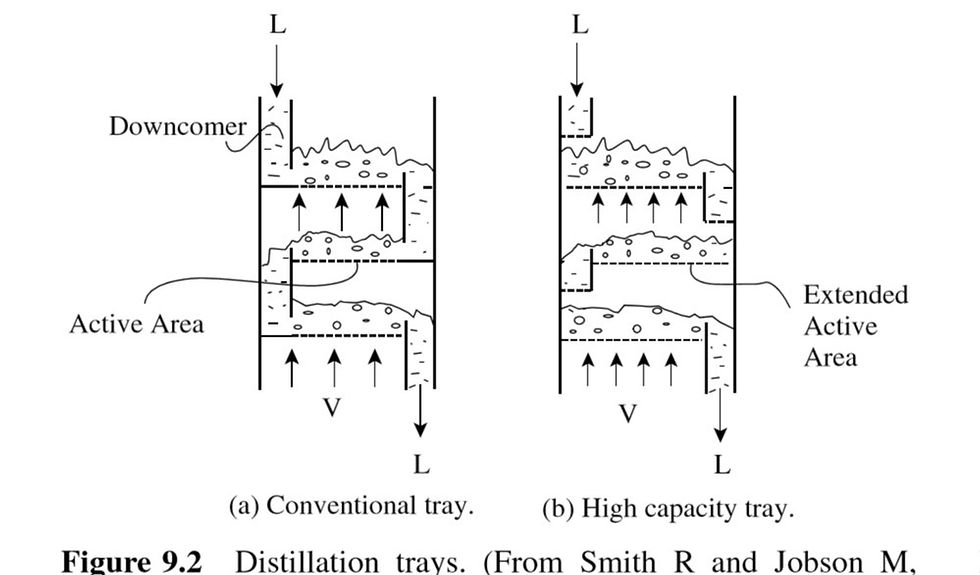
involving a plate with simple holes, known as a sieve plate, is the most common arrangement used. It is cheap, simple and well understood in terms of its performance. Many other designs of plate are available. For example, valve arrangements in the holes can be used to improve the performance and the flexibility of operation to be able to cope with a wider variety of liquid and vapor flow rates in the column. One particular disadvantage of the conventional plate in Figure 9.2a is that the downcomer arrangement makes a significant proportion of the area within the column shell not available for contacting liquid and vapor. In an attempt to overcome this, high capacity trays, with increased active area, have been developed. Figure 9.2b illustrates the concept. Again, many different designs are available for high capacity trays. In practice, the column will need more plates than the number of equilibrium stages, as mass transfer limitations and poor contacting efficiency prevent equilibrium being achieved on a plate. The other broad class of contacting arrangement for the cascade in a distillation column is that of packed columns. Here the column is filled with a solid material that has a high voidage. Liquid trickles across the surfaces of the packing, and vapor flows upward through the voids in the packing, contacting the liquid on its way up the column. Many different designs of packing are available. Figure 9.3a shows a traditional design of packing, which is random, or dumped, packing.

The random packing is pieces of preformed ceramic, metal or plastic, which, when dumped in the column, produce a body with a high voidage. Figure 9.3b illustrates structured packing. This is manufactured by sheets of metal being preformed with corrugations and holes and then joined together to produce a preformed packing with a high voidage. This is manufactured in slabs and built up in layers within the distillation column. Many types of both random and structured packing are available.
Whereas the change in composition in a plate column is finite from stage to stage, the change in composition in a packed column is continuous. To relate the continuous change in composition to that of an equilibrium stage requires the concept of the height equivalent of a theoretical plate, HETP to be introduced. This is the height of packing required to bring about the same concentration change as an equilibrium stage. Generally, trays should be used when:
• liquid flowrate is high relative to vapor flowrate (occurs when the separation is difficult);
• diameter of the column is large (packings can suffer from maldistribution of the liquid over the packing);
• there is variation in feed composition (trays can be more flexible to variations in operating conditions);
• the column requires multiple feeds or multiple products (tray columns are simpler to design for multiple feeds or products).
Packings should be used when:
• column diameter is small (relative cost for fabrication of small-diameter trays is high);
• vacuum conditions are used (packings offer lower pressure drop and reduced entrainment tendencies);
• low pressure drop is required (packings have a lower pressure drop than trays);
• the system is corrosive (a greater variety of corrosion resistant materials is available for packings);
• the system is prone to foaming (packings have a lower tendency to promote foaming);
• low liquid hold-up in the column is required (liquid holdup in packings is lower than that for trays).
BINARY DISTILLATION
Consider the material balance for a simple binary distillation column. A simple column has one feed, two products, one reboiler and one condenser. Such a column is shown in Figure 9.5. An overall material balance can be written as:
F =D+B
A material balance can also be written for Component i as:
Fx(i,F) =Dx(i,D) +Bx(i,B)
However, to fully understand the design of the column, the material balance must be followed through the column. To simplify the analysis, it can be assumed that the molar vapor and liquid flowrates are constant in each column section, which is termed constant molar overflow. This is strictly only true if the component molar latent heats of vaporization are the same, there is no heat of mixing

between the components, heat capacities are constant and there is no external addition or removal of heat. In fact, this turns out to be a good assumption for many mixtures of organic compounds that exhibit reasonably ideal behavior. But it can also turn out to be a poor assumption for many mixtures, such as many mixtures of alcohol and water. Start by considering the material balance for the part of the column above the feed,the rectifying section. Figure 9.6 shows the rectifying section of a column and the flows and compositions of the liquid and vapor in the rectifying section. First, an overall balance is written for the rectifying section (assuming L and V are constant, i.e. constant molar overflow):
V =L+D
A material balance can also be written for Component i:
Vyi,n+1 =Lxi,n,i +Dxi,D
The reflux ratio, R, is defined to be:
R =L/D
Given the reflux ratio, the vapor flow can be expressed in terms of R:
V =(R+1)D
These expressions can be combined to give an equation that relates the vapor entering and liquid flows leaving Stage n:

Figure 9.6:

CHOICE OF OPERATING CONDITIONS📌
The feed composition and flowrate to the distillation are usually specified. Also, the specifications of the products are usually known, although there may be some uncertainty in product specifications. The product specifications may be expressed in terms of product purities or recoveries of certain components. The operating parameters to be selected by the designer include:
• operating pressure
• reflux ratio
• feed condition
• type of condenser.
Pressure📌
The first decision is operating pressure. As pressure is raised:
• separation becomes more difficult (relative volatility decreases), that is, more stages or reflux are required;
• latent heat of vaporization decreases, that is, reboiler and condenser duties become lower; • vapor density increases, giving a smaller column diameter;
• reboiler temperature increases with a limit often set by thermal decomposition of the material being vaporized, causing excessive fouling;
• condenser temperature increases. As pressure is lowered, these effects reverse. The lower limit is often set by the desire to avoid:
• vacuum operation
• refrigeration in the condenser.
📌Both vacuum operation and the use of refrigeration incur capital and operating cost penalties and increase the complexity of the design. They should be avoided if possible.
📌For a first pass through the design, it is usually adequate, if process constraints permit, to set distillation pressure to as low a pressure above ambient as allows cooling water or air-cooling to be used in the condenser. If a total condenser is to be used, and a liquid top product taken, the pressure should be fixed such that:
• if cooling water is to be used, the bubble point of the overhead product should be typically 10◦C above the summer cooling water temperature, or
• if air-cooling is to be used, the bubble point of the overhead product should be typically 20◦C above the summer air temperature, or
• the pressure should be set to atmospheric pressure if either of these conditions would lead to vacuum operation.
References📖
Chemical Process Design and Integration by Robin Smith
A working guide to Process Design and Equipment by Norman Lieberman
GRAVITY SEPARATOR FUNDAMENTALS AND DESIGN by TODD B. JEKEL, PH.D.
Additional Resources 🧪🔑
You can get deep insight about Process/Chemical Engineering from these sources😉:
https://www.futurelearn.com/ Learn 100% online with world-class universities and industry experts. Develop your career, learn a new skill, or pursue your hobbies with flexible online courses.
https://www.facebook.com/SPE.BHOS - SPE BHOS arranges technical, soft skill sessions and shares a lot of quizzes, competitions and related books for petroleum and process engineering students
https://www.instagram.com/p/CAXT-ZhlrRW/ Engineerium Mentoring Center Instagram page
https://www.facebook.com/engineeriummentoringcenter Engineerium Mentoring Center Facebook page
http://www2.eng.cam.ac.uk/~mpj1001/learnfluidmechanics.org/LFM_L6.html
https://www.youtube.com/watch?v=NCvYPclQNWM Heat Exchangers Explanation
https://t.me/ebookstorage/210-Introduction to Process Engineering and Design (2015)
https://t.me/ebookstorage/211-Elementary Principles of Chemical Processes
https://t.me/OilAndGas/18122Valve Sizing Sheet
https://t.me/ebookgate/1127Engineering Fluid Mechanics Book
https://coursemania.xyz/course.html?id=433291 Free course on Fundamentals of Fluid Mechanics
https://t.me/ebookstorage/178 Engineering Heat Transfer
https://t.me/ebookstorage/159 Fundamentals of Engineering Thermodynamics (9th Edition) (2018)
https://t.me/ebookstorage/18 Heat Transfer applications and principles
https://t.me/ebookstorage/171-Design and Operation of Heat Exchangers and their Networks (2020)
https://t.me/ebookstorage/215- Industrial Separation Processes (book)
https://t.me/ebookstorage/214- Advanced Process Engineering Control (book)
https://t.me/OilAndGas- Information about Oil&Gas (mainly arabic lang)
https://t.me/chemical_worlds- Chemical Engineering Books, Quizzes and GATE Study Group
https://t.me/chemical_environmental- Discussion group related to Chemical Engineering Problems
https://t.me/chemicalengineeringworld_cew- Everything related to Chemical Engineering
https://t.me/ebookgate- Chemical Engineering E-books (Telegram Channel)
https://www.youtube.com/channel/UCqioh32NOJc8P7cPo3jHrbg- Piping Analysis
https://www.youtube.com/channel/UCQfMyugsjrVUWU0v_ZxQs2Q -Mechanics of engineered devices
http://chemicalengineeringguy.com/- suggests a wide range of courses in Chemical engineering (you can find free courses on topic of Aspen HYSYS, Aspen Plus)
https://www.youtube.com/user/LearnEngineeringTeam- suggests working principles of every engineered devices, equipment and etch.
https://www.youtube.com/channel/UCR0EfsRZIwA5TVDaQbTqwEQ- suggests great information about pumps, compressors with animation.
😋Today we have continued learning about Separation processes. Now, time to say goodbye👋🏻 until tomorrow and Stay tuned for more content 😉🌝✨!
✏️Note: If you need one of those books or links, you can contact me via my email or LinkedIn profile. #process #processengineering #engineering #chemical #chemicalengineering #technical #education #dailypost #newpost #wixsite #day29 #distillation #separation #separators #shellandtube #shell #heat #heatexchangers #design #bernoulli #technology #material #materialbalance #mass #massbalance #project #projectengineering #selfdevelopment #challenge #recycle #streams #purge #improvement #fluidflow #flow #centrifugalpumps #fluidmechanics #fluiddynamics #water #waterhammer #reliefvalves #selfactuated #contuinity #energy #equations #Pfd #processdiagrams #diagrams #piping #instrumentation #pid #development #examples #study #studentlife #fluidstatics #valves #gatevalves #globevalves #compressors
Comments